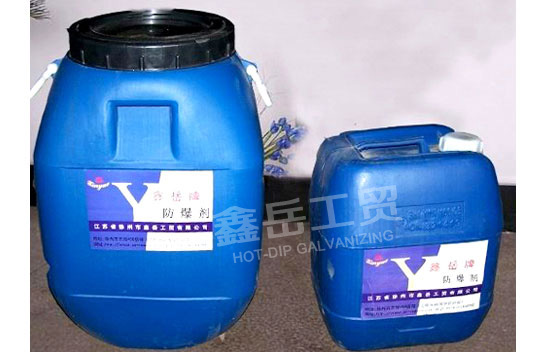
Design and Construct Hot Dip Galvanizing Plants both Domestically and Internationally
Add: Jinshan Bridge Zone, Xuzhou, Jiangsu, China
Mobile: 86-13805211808
Tel: 86-516-83168088
Email: [email protected]
The workpiece easily gets damp after being immersed in fluxing tank, because the ammonium chloride in galvanizing agent solution contains water of crystallization. And long time of dryness or buying drying equipment can solve this problem. In real hot galvanizing production, the molten zinc may splash while putting the workpiece with galvanizing agent solution on it not completely dry into zinc pot, which may results in wastage of molten zinc and endangering personal safety of workers; the traditional hot dip galvanizing adopts drying technics, which may cause low production efficiency, besides, because of beyond drying, galvanization-missing may occur and influence quality of galvanized products. For example, in hot galvanizing of cast iron and steel workpiece, this problem usually exists.
The appearance of detonation inhibitor solves the above problems, it is composed with high surface active agent and steel wetout agent, etc, which can make water spread on surface of workpiece, with no bead of water appears, and eliminate or reduce zinc explosion of workpiece. It can not only make up the shortage of preceding process, but also active surface of steel further, raise the quality of hot dip galvanizing. This is not included in other steel anti-corrosion technics. It can raise quality of galvanizing coating, reduce zinc consumption and production cost obviously by using the detonation inhibitor.
The workpiece can dry quickly after 2-5 seconds out of galvanizing agent groove if you use our detonation inhibitor, which can raise production efficiency;it can eliminate residual oxygen on workpiece, and forms a special protective layer on surface of it, which can prevent iron matrix from touching air and avoid galvanization-missing, so that the hot galvanizing process can be carried out well. The dry time of galvanizing agent can be reduced by 80% under the same temperature after adding this detonation inhibitor, and no explosion and splash of molten zinc, which can avoid waste of molten zinc and ensure personal safety of workers. Besides, it can reduce zinc ash by 20%—40%,and reduce zinc consumption obviously.
Product characters:
Add this product into fluxing tank of hot galvanizing, it has important effects as follows:
1、Reducing consumption of galvanizing agent: reduce the attached galvanizing agent on surface of workpiece, experiment shows it can save 50% of galvanizing agent.
2、Reducing solvent fog, ash and slag, which can help improve environment.
3、Improving non-uniformity of coating thickness.
4、Reducing zinc consumption, experiment shows, the average attached molten zinc on workpiece for experiment reduced by 8%.
5、Increasing coverage of galvanizing agent, prevent the workpiece after fluxing treatment from being oxidized again, reduce galvanization-missing.
6、The organic velum on surface of galvanized product can prevent zinc from oxidation, which can reduce production of zinc ash by 20%~40%.
7、Reducing water capacity of galvanizing agent, which can avoid splash of molten zinc during galvanizing.
8、Improving quality of galvanizing coating surface, this can help shorten time of dipping in molten zinc, increase brightness of coating surface.
Specifications and parameters
Appearance |
Colorless and transparent liquid |
combustibility |
incombustible |
Viscosity |
60cp(20℃) |
Boiling point |
110℃ |
Dissolubility |
At arbitrary proportion |
Ph value |
6-7 |
density |
1.17-1.19(13℃) |
Packing |
25KG/barrel |